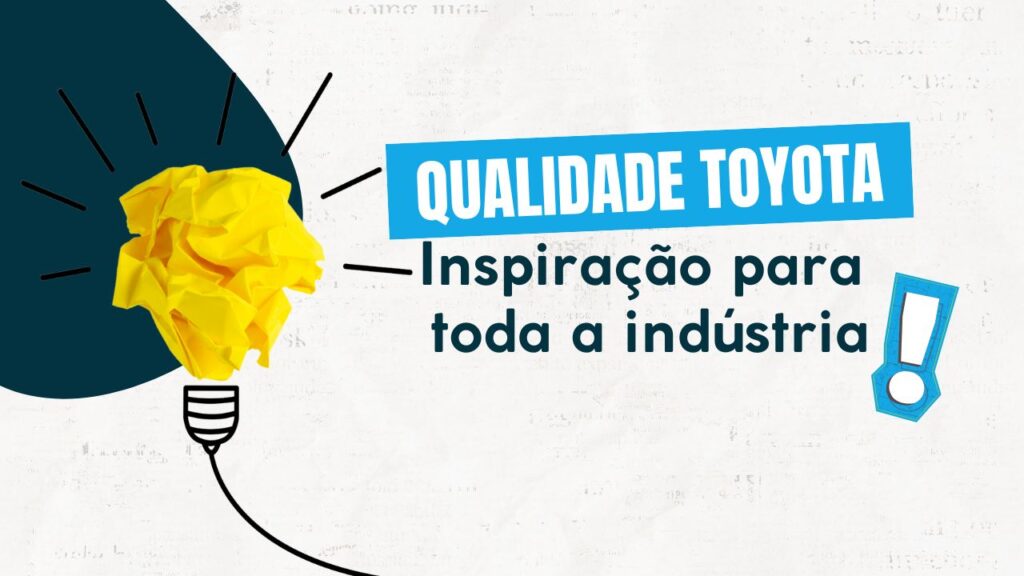
A História da Qualidade na Toyota: Do Kaizen à Revolução da Indústria Automotiva
A Toyota Motor Corporation, fundada em 1937 no Japão, não é apenas uma das maiores montadoras do mundo; ela também se tornou um pilar da história e do desenvolvimento da gestão da qualidade, transformando a indústria automotiva com seu foco em eficiência, inovação, automatização e excelência. Para entender como a Toyota construiu sua reputação global como sinônimo de qualidade, é preciso explorar suas práticas pioneiras e filosofias que moldaram a empresa ao longo do tempo.
A Base: W. Edwards Deming e o Controle Estatístico da Qualidade
Após a Segunda Guerra Mundial, o Japão enfrentava o desafio de reconstruir sua indústria. Foi nesse contexto que as ideias do estatístico americano W. Edwards Deming sobre controle estatístico da qualidade (CEP) chegaram ao país. Deming foi um dos principais responsáveis por introduzir o conceito de usar dados e processos como ferramentas para melhorar continuamente a qualidade de manufatura.
A Toyota foi uma das primeiras empresas a adotar essas práticas, liderada por intelectuais como Taiichi Ohno e Eiji Toyoda, que traduziram os princípios de Deming em estratégias adaptadas à realidade japonesa. Essas ideias formaram a base de um dos principais sistemas de gestão do mundo: o Toyota Production System (TPS).
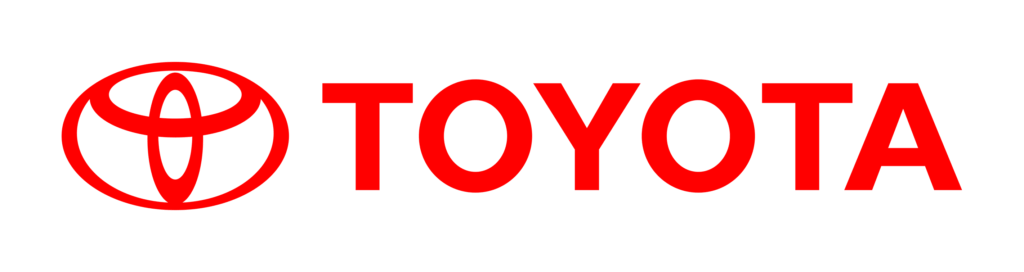
O Toyota Production System e o Nascimento do Lean Manufacturing
O TPS, desenvolvido a partir da década de 1950, revolucionou a forma como a qualidade era tratada na produção industrial. Ele integrava conceitos como:
- Just-in-Time (JIT): Produzir apenas o necessário, no momento certo, para eliminar desperdícios e reduzir estoques desnecessários.
- Jidoka (Automação): A habilidade de automatizar processos enquanto mantém supervisão humana para interromper a produção ao identificar falhas, garantindo qualidade em tempo real.
- Kaizen: O princípio da melhoria contínua, onde todos os funcionários – do chão de fábrica à alta gestão – colaboram constantemente para identificar e eliminar defeitos.
- Automatização Inteligente: O uso de máquinas avançadas que não apenas substituem o trabalho manual, mas também aumentam a precisão e a uniformidade do produto final, reduzindo significativamente margens de erro.
Combinados, esses elementos não apenas reduziram custos e otimizaram fluxos de trabalho, mas também asseguraram que a qualidade fosse mantida ou aprimorada ao longo dos processos produtivos.
A Capacidade de Inovar com Automação
Embora o conceito de Jidoka já representasse um passo importante na automação supervisionada, a Toyota expandiu suas práticas na década de 1980 ao investir fortemente em robotização e sensores inteligentes. Essas tecnologias possibilitaram a criação de linhas de montagem altamente automatizadas e integradas, onde cada etapa do processo era monitorada e ajustada automaticamente conforme necessário.
Além disso, a Toyota adotou sistemas de gestão digitalizados para conectar a cadeia de suprimentos com a produção, permitindo que alterações fossem feitas em tempo real e resultado em maior agilidade para atender às demandas dos clientes. Essa estratégia não apenas eliminou o retrabalho, mas também configurou um novo paradigma para a indústria 4.0, muito antes de ela se tornar amplamente aceita.
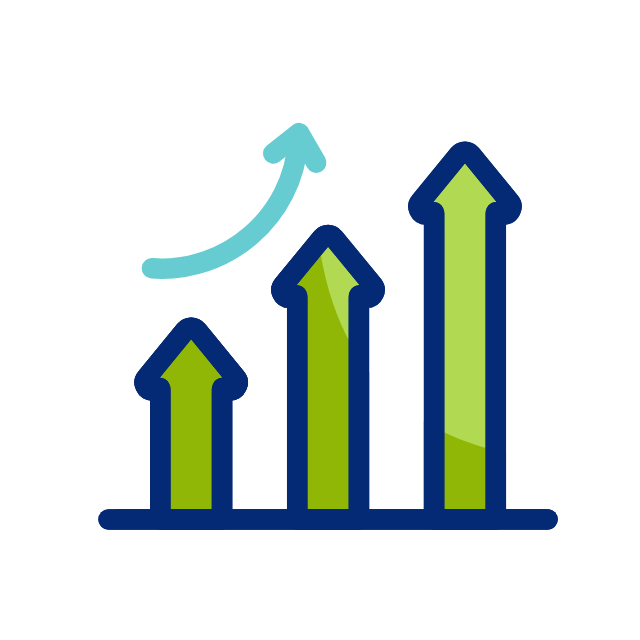
Foco no Cliente e Melhoria Contínua
Outro diferencial histórico da Toyota foi seu compromisso em alinhar a automatização às necessidades dos consumidores. Combinando ferramentas como os 5 Porquês e o FMEA (Análise de Modos de Falha e seus Efeitos), a Toyota foi capaz de criar produtos confiáveis, duradouros e alinhados às expectativas de um mercado cada vez mais exigente.
Além disso, os sistemas automatizados de feedback permitiram ajustes rápidos na linha de montagem com base nas reclamações ou demandas, assegurando que os veículos entregues mantivessem o padrão de excelência da marca.
Qualidade e Sustentabilidade na Era Digital
Nos últimos anos, a Toyota renovou seu compromisso com qualidade e automação ao investir em tecnologias de ponta para criação de veículos híbridos e elétricos. O desenvolvimento de modelos como o famoso Prius contou com processos totalmente digitais e automatizados, permitindo maior precisão e eficiência na fabricação – tudo com um foco profundo na sustentabilidade ambiental.
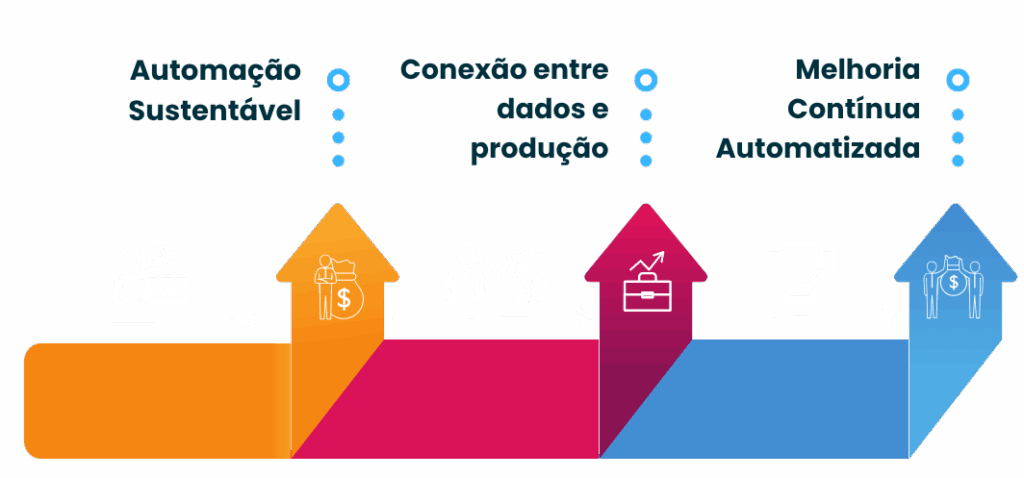
1. Automação Sustentável
A implantação de tecnologia deve ser feita de forma inteligente, sem perder o foco no papel fundamental das pessoas no aprimoramento dos processos.
2. Conexão entre dados e produção
Tecnologias que integram dados em tempo real com manufatura são essenciais para garantir flexibilidade e qualidade absoluta.
3. Melhoria Contínua Automatizada
A automação não elimina a necessidade de Kaizen; ao contrário, potencializa a inovação quando usada estrategicamente.
A Toyota é um exemplo vivo de como a automação e a tecnologia podem ser integradas à cultura de melhoria contínua para atingir padrões de qualidade excepcionais. No cenário atual, em que a indústria 4.0 se torna o novo padrão, o modelo Toyota continua sendo uma inspiração para organizações de todos os portes que buscam conquistar mais eficiência, construir processos sólidos e, acima de tudo, entregar excelência ao cliente com responsabilidade e inovação.